Work order process overview
After you create a work order, you can modify it without regard to the routing that was used to create it. If permanent changes are required, they should be made to the routing. If temporary changes are required, those changes should be made to the individual work order.
After the application populates the configuration screens with the correct data, the screens are no longer required for normal work order processing. Work orders are either downloaded from a host system or manually created by warehouse associates using the adding a work order feature. The chart below describes the process flow for work orders.
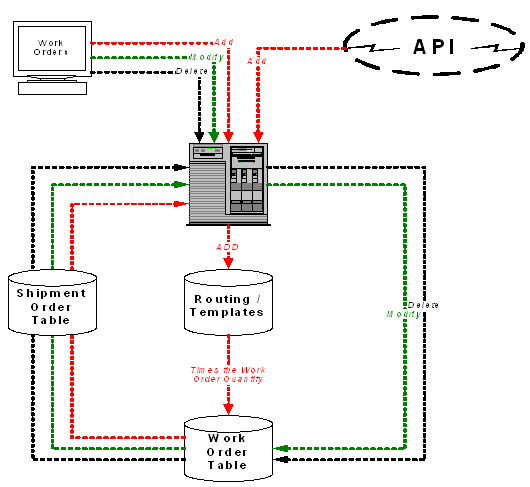
When a work order is added or downloaded, the application:
- Finds a routing record for the parent item
- Multiplies the routing quantities by the quantity of the work order
- Builds the work order records
- Creates shipment orders and assigns the Component order type for the components required by each operation. Multiple shipment orders are created if multiple owners are included in the bill of material components.
When a work order is modified, the application:
- Modifies work order records
- Updates component orders to reflect the changes.
When components are added to an operation, the application:
- Modifies work order records
- Updates component orders to reflect the changes
- Adds new component orders when necessary
- Requires change to a Joins Components operation type if components are added to a previously Does Not Change Inventory operation.
When components are deleted from an operation, the application:
- Modifies work order records
- Updates component orders to reflect the changes
- Automatically ships component orders at the completion of the operation.
When a work order is deleted, the application:
- Deletes work order records
- Deletes associated component orders.
- The application does not currently support adding or deleting entire operations from the work orders. The application displays an error message if you attempt to do this.
- Work order bill of materials and routing templates can be created dynamically from an imported shipment order. Order detail lines with a line type of C (component) are used to create the BOM and template. These lines are then removed from the order. If parent kit item stock is insufficient, you can create a work order to build the kits using the dynamic BOM and template.