Details Fashion
Infor M3 Planning Workbench (Infor M3 PWB) is available in three industry variants:
- Fashion
- Food and Beverage
Equipment
Infor M3 PWB has four key elements:
- Supply Chain Orders. A generation of a chain of linked orders to meet demand.
- Macro Orders. Aggregation of orders for planning purposes.
- Planning Workbench. A desktop decision support application for planners.
- Action Log. A closed loop system for managing and implementing decisions.
Supply Chain Orders – Linking Order Chains
M3 Supply Chain Orders was designed to improve the way an organization plans and manages order chains by pegging orders. Supply Chain Orders can apply from a complex multi-facility manufacturing supply chain to a single site label-to-order operation.
Supply Chain Orders improve global visibility, deliver information quicker and automate quantity and date changes. This leads to improvements in on-time deliveries, lower inventories, less manual work and a more agile and chaos tolerant supply chain.
Flexibility
Supply Chain Orders are generated online based on user-defined rules when a customer order is specified or a distribution order is released. Generation of multilevel dependent demand on a lot-for-lot basis improves decision making, prioritization, and the execution of activities such as ordering, allocation and manufacturing.
Supply Chain Orders may co-exist with Material Requirements Planning (MRP) so that an item may, for example, be MRP planned against the forecast until the entry of a customer order triggers the creation of a Supply Chain Order chain. This is a major advantage over existing back-to-back order-initiation techniques.
Policy rules determine the strategy for the generation and management of Supply Chain Orders. You can define different strategies for different items, so that you might control some products on an end-to-end Supply Chain Order, while for others you may use several different Supply Chain Orders to represent different stages of production or you may use MRP for part of the chain and Supply Chain Orders for other parts. If required, you can manually override the automatic rules.
Any existing inventory or orders without demand can optionally be considered when generating a Supply Chain Order chain. In these cases, existing inventory or orders are used as a priority instead of creating lot-4-lot orders.
This diagram shows an example of how Supply Chain Orders can be used in an apparel manufacturing environment. In the diagram, three supply chain orders are used, fabric, cutting and sewing, respectively, but it could all be defined as one.
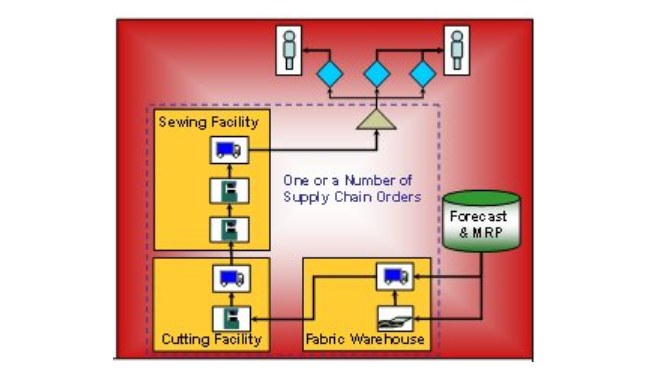
- Forecast for longer-term planning.
- MRP drives fabric purchasing.
- Customer contract or distribution orders triggers supply chain orders.
- Supply chain orders covers from demand through sewing and cutting to fabric supply.
Simplicity
Supply Chain Orders enhance visibility and simplify the tracking of linked order chains. The unique reference ID enables the status of a Supply Chain Order chain to be quickly determined and supports a Seiban approach. This enables planners to focus on the critical issues and to see the consequences at the end item level.
Supply Chain Orders simplify and remove significant manual work from the process of implementing changes to dates and quantities or altering the manufacturing facility for a customer order.
Automation
The hard linking, or pegging, of orders combined with the policy rules enables more auto-mated implementation of downstream changes to quantities and dates and upstream changes to quantities by propagating the changes through the order chain. For upstream changes, user-defined rules determine whether only increases or decreases or both are permitted.
A tolerance handling option allows user-defined rules for how both upstream quantity changes and shortage situations in MRP are handled. Within the tolerance level the related orders are adjusted appropriately. If the change is outside the tolerance threshold, new orders are created or product held as inventory. For example, there are two customer orders each requiring 100 pieces, so a purchase order is generated for 200 pieces. Nevertheless, the supplier delivers 225 pieces. As the tolerance on the first customer was +/-!0% and on the second +/-20%, the order network is automatically modified to supply 110 pieces to the first customer and 115 to the second. Another example could be where the demand was for 100 pieces +/-10% and only 80 were received. In this case, as the delivery was outside the tolerance, a new order would be created for 20 pieces.
Actions messages provide proactive flagging of exception conditions/potential problems to planners, so that they can make appropriate and timely decisions.
Supply Chain Orders versus MRP and Order-Initiated
MRP | Order-initiated | Supply Chain Orders | |
---|---|---|---|
Order Generation | No supply chain relation is exploded | Supply chain relation can only be exploded using released orders | Supply chain relation is triggered by a customer order or released distribution |
Relationship between Demand and Supply | No direct relations between demand & supply | Only 1-to-1 relation between demand & supply | Can have multiple relations between demand & supply |
Explosion of Supply Chain Relations | No supply chain relations are exploded | 1-directional supply chain relation explosion only – top-to-bottom | 2-directional supply chain relations explosion – top-to-bottom or bottom-to-top |
Order Linking | No links unless preallocation links created manually | Automatic links based on fixed condition | Automatic linking based on user defined policy conditions |
Use of Existing Stock or Orders | Always considers available supply (stock or orders) | Available supply (stock or orders) are never considered – always creates new supply order | Have option to consider available supply (stock or orders). More efficient supply management |
No link at all between demand & supply unless preallocation is used | Semi hard link – relation can be broken and network rebuilt at any time base on the best scenario | Hard link – relations must be broken manually |
Macro Orders – Working at an Aggregated Level
Macro Orders are a new concept that aggregates manufacturing orders and proposals on the M3 BE for planning purposes. The aggregation is based on user-defined criteria.
Macro Orders dramatically reduce the number of orders for planning and significantly improve simulation performance during planning, and the time for loading data into a memory-resident simulation environment.
- Flexibility
Macro Orders can be created at the style or style/color level. The Macro Order setup sup-ports different timeliness and bucket lengths to control the size/number of Macro Orders.
Only materials and operations defined as critical are included in Macro Orders and they can optionally be limited to a customer or customer order.
Macro Orders can be created at different grouping levels for preliminary and firm planned orders. For example, preliminary orders at the style level and firm planned orders at the style/color level.
- Simplicity
Viewing of data and plans at an aggregated level makes it easier to get an overview of the plan at an appropriate level for planning purposes.
Macro Orders combined with the Planning Workbench make it easy to quickly move groups of SKU level orders between facilities and manufacturing lines.
- Automation
Macro orders are generated automatically, which means the planner does not must spend additional time and work creating them.
Planning Workbench - Decision-Making
M3 PWB is designed for fashion manufacturers and food and beverage manufacturers, respectively, that need to balance load across one or more sites and generate effective line plans at, for example, the style or style/color level. It is a decision support tool to help planners improve the way their organization utilizes its capacity to meet customer delivery dates.
Planning Workbench enables medium term capacity and subcontracting. Unlike in spreadsheets, the real world constraints, rules and latest decisions are considered. Planning Workbench is tightly integrated with the rest of M3, which means the impact of decisions are reflected in other applications such as Supply Chain Execution and Finance.
The simulation capabilities of Planning Workbench provide early visibility of potential delivery issues for more proactive decision-making and better prioritization. This can lead to improvements in on-time delivery performance, enhanced customer service and greater responsiveness to changing customer demands. Effective decision making in Planning Workbench means more effective use of production resources that in turn results in inventory reductions, lower labour costs and lower planning resource requirements.
- Flexibility
The Planning Workbench can allow, for example, planning at one level, such as style, on preliminary orders and another level, such as style/color, on firm planned orders. Further flexibility in terms of user controlled data aggregation and sorting is provided for re-porting purposes so you can view by, for example, category or range. The capacity unit for planning can be based on pieces or time.
Planning Workbench supports a multiple planner environment. Roles determine the time periods and facilities across which a planner can make decisions – "the decision window".
- Simplicity
Planning Workbench is a central workbench for decision making during the production planning process. Its intuitive graphical user interface, flexible grouping, industry "look and feel" and built in simulation capabilities make decision making much easier. Planning can become fun, instead of a tedious chore.
- Automation
Planning Workbench can enable planners to easily and quickly move macro orders (aggregated order groups) between facilities or resources and determine the consequences in terms of material availability, capacity utilization and delivery capability. It also supports decisions such as subcontracting, moving macro orders in time or splitting macro orders.
Action Log – Implementing Decisions
The Action Log is for managing and implementing the decisions made in Planning Workbench. Unlike spreadsheets and many other planning applications, the planning decisions are logged and a status is maintained against them. This enables two key things:
- Line Supervisors can see any decisions on which they must take action such as increasing the capacity on a production line by 50% for a two week period; and
- It closes the loop between planning and execution so that the status of implementing decisions is taken into consideration in the next planning cycle.
There are some planning decisions that it is not easy to automatically implement. For example, you may know that you must add capacity on a production line, but how should you implement the decision. The line supervisor may decide that operators should work overtime, or to add machines to the line (from an under utilized line), or add an extra shift, etc.
- Flexibility
The Action Log is a concept that makes it easier for both planners and supervisors to work together to make and implement decisions. The Action Log provides a traceable history of decisions. Each decision/action has a number, a person responsible and a status against it.
- Simplicity
The decision life cycle ensures information and integrity in decision making between planning cycles.
- Automation
The decisions that can be implemented in an automated way, such as reschedule, are automatically executed when decisions are transferred from Planning Workbench. Those that cannot be implemented automatically are handled by supervisors.