Location assignments
Location numbers must identify a location to facilitate picking, putaway, and other processes that interface with a location. For example, you might begin by identifying the aisle pattern. After you number the aisles, you can identify each section of shelving as a bay number. Within the bay, the numbering recommendation is from bottom to top, and left to right.
Another numbering convention is bottom to top, closest to aisle to farthest from aisle. Therefore, the high velocity bins are closest to the center pick aisle. After the bays are numbered, you determine the number of shelves or levels in the bay, beginning with the closest shelf to the floor. Going vertically across a shelf, determine the maximum number of bins, or slots, that you can fit on the shelf.
These bins or slots are the locations that must have bin location labels printed. These location-numbering schemes are both independent of zones. These schemes enable you to reconfigure zones without affecting the location numbering system. You can adapt the warehouse to changes in these methods as your business changes:
- Picking patterns
- Picking techniques
- Size requirements
This diagram shows a section of a warehouse and an example of the location IDs:
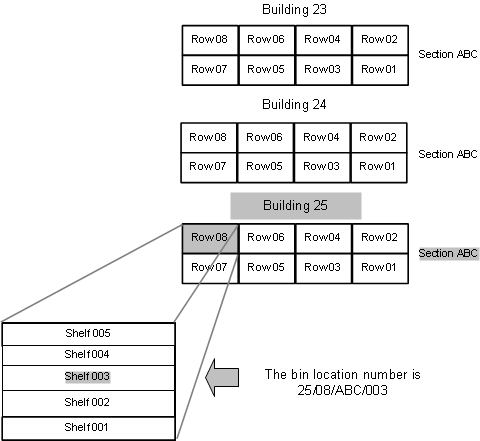
Within the aisles, the bays represent sections odd or even numbers, depending on the side of the aisle the bay resides.
Within the bay, each level of shelving is assigned a number with the lowest number closest to the floor.
Within the levels are the bins or slots in which products are stored. Each bin must have a location label specified to identify and associate the bin with the product stored within.
The layout that works best for your particular operation is different than the layout of any other warehouse. Be consistent when you are assigning your location IDs.